The 7 Problems with a Poorly Serviced Hydraulic Power Unit (HPU)
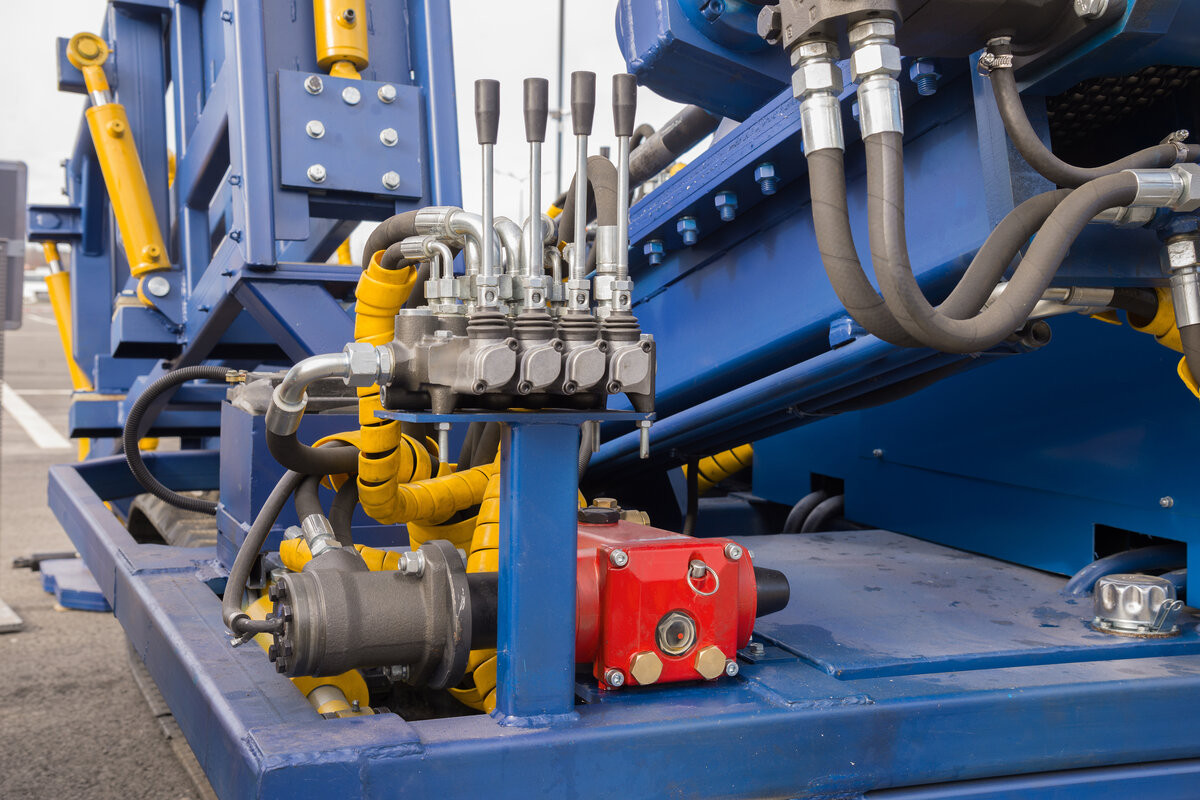
We see a lot of faulty Hydraulic Power Units (HPU) that have stopped, simply because they weren’t serviced correctly. The HPU plays a critical role in systems that rely on hydraulic power. It provides the necessary force to drive hydraulic cylinders, motors, and other components essential to a wide range of industries, from manufacturing to construction and aerospace. However, when an HPU is poorly serviced, or even worse, never serviced, it leads to bad things happening – such as expensive downtime, equipment damage, and dangerous work conditions. Below are the seven key problems that arise when you have a poorly serviced hydraulic power unit.
1. Decreased System Efficiency
The biggest sign of a poorly maintained HPU is a noticeable drop in system efficiency. Hydraulic systems rely on a clean, high-quality hydraulic fluid to maintain pressure and deliver power. Over time, contamination from dust, dirt, moisture, or even worn internal components can infiltrate the fluid. A clogged or worn filter, if left unchecked, will allow contaminants to circulate through the system, causing components to work harder and run inefficiently. This leads to increased power consumption, lower output, and inconsistent operation.
Common Signs:
Slower actuator response times
Irregular or fluctuating pressure levels
Overheating or excessive noise from the unit
2. Increased Wear and Tear on Components
Hydraulic systems are built with precision, and any deviation in operating conditions—such as poor fluid quality, improper pressure, or uneven load distribution—means that ‘things’ (seals, valves, and pumps) will wear out a lot faster. A poorly serviced HPU will inevitably lead to costly repairs, or replacements. But most importantly, interrupted workflow and production downtime.
Common Signs:
Premature seal or gasket failures
Abnormal wear patterns on hydraulic pistons and cylinders
Frequent valve malfunctions or pump failure
3. Hydraulic Fluid Contamination
Contaminated hydraulic fluid is a killer of any hydraulic system. Whether caused by a failing filter, the intrusion of dirt, or internal corrosion, dirty hydraulic fluid can wreak havoc on an HPU. Contaminants will clog valves, damage seals, and erode sensitive components. Regular fluid analysis and filter changes are necessary to prevent contamination from spreading.
Common Signs:
Darkened or milky hydraulic fluid
Metal shavings or particulates in the fluid
Increased system pressure or overheating
4. Overheating and Temperature Fluctuations
An improperly serviced HPU may develop overheating problems, often due to clogged filters, insufficient fluid levels, or poorly maintained cooling systems. High temperatures can reduce the viscosity of hydraulic fluid, making it less effective in transmitting power and increasing the likelihood of leaks. Plus, it will damage seals, gaskets, and hoses—and ultimately stop the hydraulic pump and motor.
Common Signs:
Persistent high fluid temperature readings
Fluid leaking from seals and connections
Burnt smell from overheated components
5. Hydraulic Leaks
Leaks are a clear sign of an HPU that is in disrepair. A well-maintained system should have tight seals and properly connected hoses. But when maintenance on the HPU is neglected, seals can become worn or brittle, and connections can loosen. Hydraulic leaks not only waste expensive hydraulic fluid but also reduce system pressure and can create a slippery and dangerous work environment.
Common Signs:
Visible pools of hydraulic fluid around the unit
Loss of pressure in the system
Oil spots or slick surfaces near hydraulic components
6. System Failures and Downtime
The culmination of the issues above can lead to the ultimate problem: complete system failure. Whether due to worn-out components, fluid contamination, or overheating, a failure in a hydraulic system can cause significant downtime. This is especially problematic in industries where machinery needs to run continuously to meet production targets. Equipment failure can be unpredictable, and when it happens, it often results in costly repairs and missed deadlines.
Common Signs:
Sudden loss of pressure or power
Equipment stopping mid-operation
Alarms or emergency shut-off triggers
7. Safety Risks
Neglected hydraulic systems can present serious safety risks. Hydraulic fluids under high pressure can be hazardous if a hose or seal suddenly fails. Leaks can lead to slip hazards, and overheating components can pose fire risks. Furthermore, a sudden loss of hydraulic power during operation can endanger workers who may be handling or operating heavy machinery, such as lifts or presses.
Common Signs:
Frequent emergency stops or safety shut-offs
Pressure spikes or unexpected power loss
Excessive wear on load-bearing components
Preventive Measures:
To avoid the costly and dangerous problems associated with a poorly serviced HPU, regular preventive maintenance is crucial. Here are some best practices to ensure the longevity and efficiency of your hydraulic power unit:
Regular Fluid Checks: Monitor hydraulic fluid levels and condition, and replace the fluid when necessary.
Filter Changes: Replace or clean filters on a regular schedule to prevent contamination from spreading.
Leak Inspections: Frequently inspect hoses, seals, and connections for signs of wear or leaks.
System Testing: Regularly test pressure levels, system efficiency, and operational soundness to catch problems early.
Temperature Control: Ensure the cooling system is functioning properly and monitor the operating temperature of the hydraulic unit.
Conclusion
A hydraulic power unit is the heart of any hydraulic system, and neglecting its maintenance can lead to a host of problems, including decreased efficiency, component wear, fluid contamination, overheating, leaks, and even system failure. By performing regular service and maintenance, you can ensure that your HPU runs smoothly, minimises downtime, and reduces safety risks, ultimately saving time and money while maximising productivity.